Mechanical Microscopy is the next step in the evolution of nanoindentation. It offers a powerful new way to simultaneously characterize the relationships between materials’ microstructure and various mechanical properties using high-speed nanoindentation mapping.
Using FemtoTool’s unrivaled force sensing technology, Mechanical Microscopy reveals trends in properties like Hardness and Modulus over a wide range of length scales from centimeters to microns.
By combining this technique with environmental testing and correlative electron microscopy techniques, Mechanical Microscopy allows the complex relationships between structure, properties, and performance to be directly determined as never before.
Application examples
- 01 Cast Irons
- 02 Nuclear Materials
- 03 Multi-Phase Microstructures
- 04 Heavily-Deformed Microstructures
- 05 Additive Manufacturing
- 06 Coatings & Surface Treatments
- 07 High Resolution
- 08 Cold Spray
- 09 Laminate Materials
- 10 High Loads/Large Areas
High Chromium Cast Irons
High chromium cast irons, or white cast irons, are widely applied in the mining, milling, earth-handling, and manufacturing industries due to their exceptional wear and corrosion resistance. These properties result from the mixture of the material’s ductile iron matrix and high fraction of hard carbide phases.
In this example, Mechanical Microscopy was applied to investigate the influence of different heat treatments on the microstructural evolution of the hard phases. The native displacement control of FemtoTools systems provided uniform characterization even with the 5× difference in hardness between the phases!
51,200 Indentations |
Nuclear Materials
Nuclear materials face uniquely challenging environments. Embrittlement caused by hydride precipitates in zirconium claddings constitutes a significant risk factor for the integrity of spent nuclear fuel rods. Mechanical microscopy enables high resolution characterization of local mechanical properties changes caused by hydride formation.
In this example, hydrides in Zircaloy-2 were investigated in collaboration with the Paul Scherrer Institut (PSI). High resolution neutron radiography and mechanical microscopy were demonstrated to identify and quantify the local concentration of hydrogen/hydrides along the clad wall. Read more at the Journal of Nuclear Materials 584 (2023) 154574.
57,600 Indentations |
Multi-Phase Microstructures
Extracting the properties of individual phases within a microstructure is an essential part of determining its behavior. Ensuring that these results are truly representative of the phase’s behavior is challenging when the number of indentations is small. Mechanical Microscopy enables the statistical determination of phase-level properties from maps with thousands of datapoints.
In this example, a two-phase, eutectic alloy consisting of aluminum alloyed with copper and an Al2Cu intermetallic phase is characterized by Mechanical Microscopy. Despite the material’s fine-scale micro-structure, the properties of the two phases are clear and distinct in the 2D histogram.
51,200 Indentations |
Heavily-Deformed Microstructures
Heavily-deformed materials can feature high levels of internal plastic strain. This increases their strength, but it makes them challenging to characterize using techniques such as electron-backscatter diffraction (EBSD). Mechanical microscopy provides a high-resolution solution for characterizing these materials.
In this example, Mechanical Microscopy reveals local dislocation density increases along preferential slip planes within grains of a cold-rolled 316L stainless steel. This deformation increases local disorder, which causes significant local reduced modulus variation, in addition to hardening. This provides valuable information on strain hardening behavior.
200 nm Indentation depth |
Additive Manufacturing
Additive Manufacturing methods are transforming modern manufacturing by enabling easy fabrication of complex 3D part geometries with novel microstructures. Mechanical Microscopy reveals the effects of these new processes on the local mechanical behavior of these microstructures, allowing better optimization of processing parameters.
In this example, a 316L steel sample made by laser powder bed fusion (L-PBF) is viewed in cross-section. This reveals the columnar fish-scale microstructure formed by adjacent melt pools in the build direction as well as defects like pores and hardening at melt-pool boundaries.
2 µm |
Coating & Surface Treatment Characterization
Nanoindentation is a key technique for analyzing coatings and surface treatments, utilizing top-down indentation for thin films and cross-sectional indentation for thicker coatings. Mechanical Microscopy transforms this from simple line plots to high resolution maps of mechanical property variations through the coating thickness.
In this example, Mechanical Microscopy reveals the local properties within a hard anodized coating on a 5052 aluminum alloy. Mechanical property maps reveal porosity, cracks, a denser adhesion layer at the aluminum interface, and a gradient in hardness and modulus towards the coating's surface.
100 nm Indentation depth |
High Resolution Mapping
Mechanical microscopy can be applied over a wide range of length scales, including extremely small depths, enabling high-resolution characterization of microstructures. This enables even sub-micron microstructural features to be accurately characterized.
In this example, the Pearlitic microstructure of a medium carbon steel is examined with a lateral resolution of 250 nm. This exceptional resolution allows the visualization of individual Cementite lamella within the Pearlite grains. These are so narrowly spaced that they diffract light, giving the phase its namesake pearlescence. Using the industry-leading sensitivity of FemtoTools systems, even these features can be resolved.
250 nm Indent spacing |
160'000 Indentations performed |
Cold Sprayed Materials
Materials formed by cold spray feature high levels of internal plastic strain due to the severe plastic deformation processes experienced by the individual splats as they accumulate to form the coating. This increases their strength, but it makes them challenging to characterize using techniques such as electron-backscatter diffraction (EBSD). Mechanical microscopy provides a high-resolution solution for characterizing these materials.
In this example, Mechanical Microscopy reveals inter-splat boundaries, local porosity, and defects within a sample of cold-sprayed 316L stainless steel. This provides valuable information for optimizing processing parameters.
200 nm Indentation depth |
Laminate Materials
Accumulative roll bonding (ARB) is an attractive way to manufacture metal nanolaminate materials at bulk scale. By repeatedly rolling, cutting, stacking, and rolling again, ARB processing can generate large sheets of material with nano-scale laminate layers. These materials can have astonishingly high strengths and tailored properties.
In this application example, an Fe-Bronze laminate manufactured at FAU Erlangen by M. Ghanem and Prof. B. Merle in the group of Prof. M. Goeken is investigated using mechanical microscopy. This reveals the influence of texture evolution in the Fe layer and the success of the intermediate annealing treatment on the Bronze layer.
51,200 Indentations |
Large Area Mapping
Mechanical microscopy can be applied over a wide range of length scales, including higher forces over large areas. This allows mechanical property variations over the millimeter and centimeter scale from manufacturing processes and heat treatments to be rapidly characterized.
In this application, with the Seita group (formerly at NTU, now Cambridge), designed mechanical property variations were printed into the material using a novel binder-jetting additive manufacturing technique followed by sintering. Both the designed variations and ripples from the metal powder layer density variations can be clearly observed. Read more at Materials & Design 235 (2023) 112384.
2 N Maximum force |
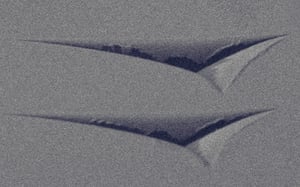
Nanoindentation
READ MORE ->
Read More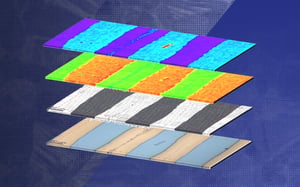
Correlative Mechanical Microscopy
READ MORE ->
Read More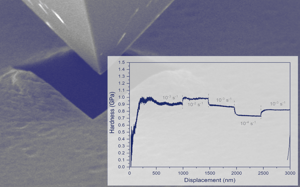
Strain-Rate Control
READ MORE ->
Read More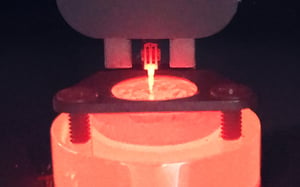
High-Temperature Testing
READ MORE ->
Read More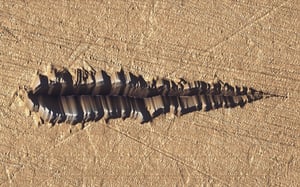
Scratch Testing
READ MORE ->
Read More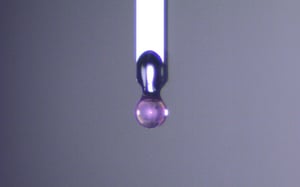
Soft Materials Testing
READ MORE ->
Read More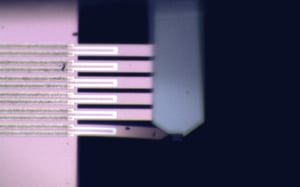
MEMS Mechanical Testing
READ MORE ->
Read More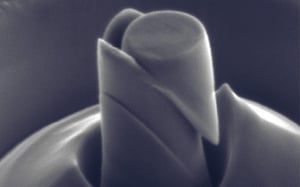
Micro-Pillar Compression
READ MORE ->
Read More