Nanoindentation is the most advanced form of hardness testing. Pioneered by Oliver and Pharr in their seminal paper in 1992, the nanoindentation technique allows the automated measurement of both hardness and elastic modulus.
Their innovation removed the need for measuring the size of the residual indentation by using contact mechanics to determine the indentation size from the force-displacement curves measured during the test.
Nanoindentation has since evolved into the most advanced mechanical characterization technique for materials with test modalities now able to accurately measure nearly every type of mechanical property.
Application examples
- 01 Nanoindentation Modalities
- 02 Simple Nanoindentation
- 03 Continuous Stiffness Measurement (CSM)
Nanoindentation Modalities
Since its invention, nanoindentation has become the most widely used mechanical test in the world. It has been used to probe a wide variety of different mechanical properties on nearly every class of material. Nanoindentation is most often used to probe quasi-static properties: hardness/strength and elastic behavior. However, this is only the beginning.
Nearly every mechanical property of materials can be investigated using indentation. Dynamic, time-dependent, and cyclic properties of materials can be probed using a variety of techniques. Even complex properties such as fracture behavior and phase transformations can be measured using nanoindentation. This versatility makes a nanoindenter an essential tool for your laboratory.
Simple, Monotonic Nanoindentation
Simple Indentation (SI) is sometimes the most powerful nanoindentation method. In this method, the indentation is performed using a monotonic load/unloading path without dynamic oscillations. This can be performed using linear or quadratic loading/displacement rates and with constant indentation strain rates.
In this mode, the unmatched dynamics of the FemtoTools’ systems are used to passively measure the dynamic mechanical response of the material to simple loading. This allows discrete events during the test, such as cracking or intermittent plasticity, to be characterized in high detail.
Continuous Stiffness Measurement (CSM)
Why perform hundreds of simple nanoindentations when you can perform thousands of measurements within a single nanoindentation test? This is the power of the Continuous Stiffness Measurement (CSM) technique for nanoindentation. In a simple, monotonic nanoindentation only one stiffness measurement is performed during unloading.
In this mode, during a CSM test, a dynamic oscillation is superimposed during loading, which allows stiffness measurements to be made continuously during the test. This allows Hardness and Modulus to be measured as a function of penetration depth during each indentation. With FemtoTools’ industry leading force and displacement precision, these oscillations can be performed at small fractions of a nanometer, allowing high-speed CSM measurements even at shallow depths.
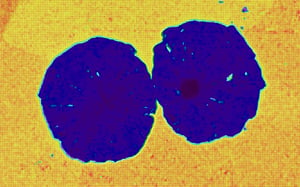
Mechanical Microscopy
READ MORE ->
Read More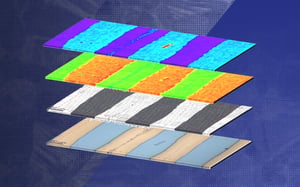
Correlative Mechanical Microscopy
READ MORE ->
Read More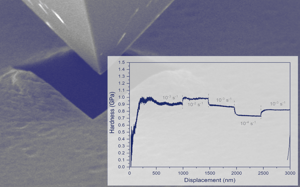
Strain-Rate Control
READ MORE ->
Read More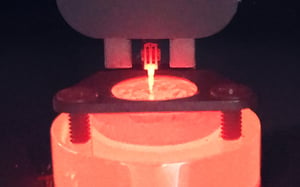
High-Temperature Testing
READ MORE ->
Read More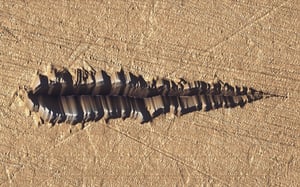
Scratch Testing
READ MORE ->
Read More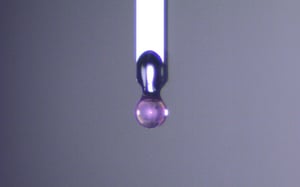
Soft Materials Testing
READ MORE ->
Read More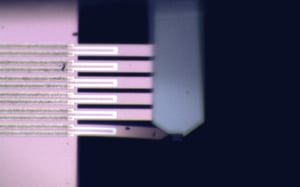
MEMS Mechanical Testing
READ MORE ->
Read More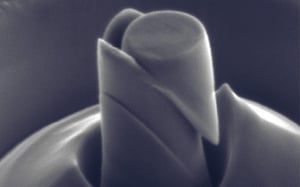
Micro-Pillar Compression
READ MORE ->
Read More